Process Qualification & Calibration
Optimizing Repeatability in AM: The Role of Qualification and Calibration
As a Quality Engineer, the routine calibration and qualification processes are essential to ensure the repeatability and predictability of production over time. This encompasses maintaining parts at an acceptable standard and ensuring 3D metal printing machines like Aconity3D, EOS, Renishaw, SLM, and others, perform within specified parameters. Achieving manufacturing repeatability requires the qualification of the process, machine, and parts, along with a thorough understanding and management of variables. Qualification and calibration outputs play a crucial role in ensuring that (a) the setup remains consistent and (b) the outputs stay within acceptable tolerances from one build to another.
Qualification and calibration processes are often resource-intensive and costly. In industries employing metal additive processes, qualifying a new material from scratch can involve expenses of up to a million dollars and can take several years to complete. Testing is required across various power, speed, strategy, and layer thickness ranges for each print that needs to be dissected. Samples must undergo testing for porosity, material properties, fatigue in both low- and high-cycle conditions, conducted over hundreds of thousands of cycles until failure, as well as other mechanical tests under a wide range of thermal conditions.
Dyndrite LPBF software automates tasks such as build layout, parameter assignment, labeling, and logging, reducing setup and verification times by immeasurable amounts.
- Available materials (new materials, multi-material)
- Printable parts (small features, thin walls etc.)
- Quality of parts (material homogeneity, surface profile)
- Whether or not the process requires aids such as supports
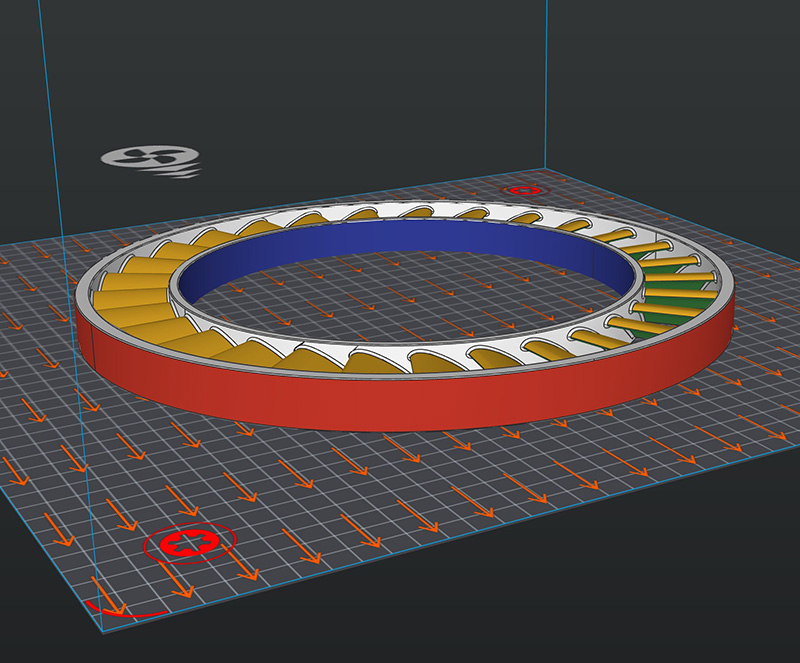
Qualifying the printing process itself starts with determining material property targets, agreeing on how components will be qualified, and what technologies will be used to determine acceptance.
Qualification of a machine begins with producing test specimens so that "performance-based data" can be generated that shows the machine can produce components that meet design intent. Process variables must be controlled, such as build chamber atmosphere, fusion parameters like layer thickness power, and scan speed. The part material properties used as a target must come from the design engineering community. The goal is to create specimens that meet design intent from the perspective of material strengths. Next, the machine produces a component that is later inspected for validation. A new part’s planned toolpath/thermal time history may be evaluated to ensure the entire process fits within design bounds for the process being applied. The machine must show the ability to produce the same material property results over the duration of the build process, and must be re-validated on a regular schedule. This means that the qualification and calibration process is a regular and repeated part of the manufacturing process.
A specimen qualification build shows whether material properties of sample components change with build box position (along x, y, and z planes), with build volume, with the build tool (light engine source/printhead/laser), and over repeated builds.
- Available materials (new materials, multi-material)
- Printable parts (small features, thin walls etc.)
- Quality of parts (material homogeneity, surface profile)
- Whether or not the process requires aids such as supports
To capture and qualify specimen characteristics, engineers must qualify the entire stroke of the machine, including (Z height) and across both the build plate width (X) and length (Y). Test builds are intentionally built with the maximum number of specimens to maximize the production build area and duration. Builds also often include material capture vessels in each corner of the build plate to capture material that can be analyzed for chemistry after the formation. The red area represents the tool overlap (stitching) area, where multiple tools may affect the manufacturing process. In binder jetting this may mean printhead overlap areas, or nozzle overlaps for redundancy. In photopolymerization this means multiple light engines being used to cover the whole build area.
Once printed, these specimens are then measured for relevant properties, and their mechanical properties are stored in a database.
Once a machine has been qualified, part qualification is performed by printing test specimens inside, next to, or onto a part. Mechanical properties of these specimens must match the material properties of the process database within an agreed on level of tolerance. This type of part acceptance testing will continue during production runs to ensure part consistency.
- Available materials (new materials, multi-material)
- Printable parts (small features, thin walls etc.)
- Quality of parts (material homogeneity, surface profile)
- Whether or not the process requires aids such as supports