Production Overview
The Two Pillars To Production Success
There are two key pillars to production success: traceability and repeatable quality. Legacy additive manufacturing has faced challenges in scaling to production due to non-compliance with these critical pillars.
- Available materials (new materials, multi-material)
- Printable parts (small features, thin walls etc.)
- Quality of parts (material homogeneity, surface profile)
- Whether or not the process requires aids such as supports
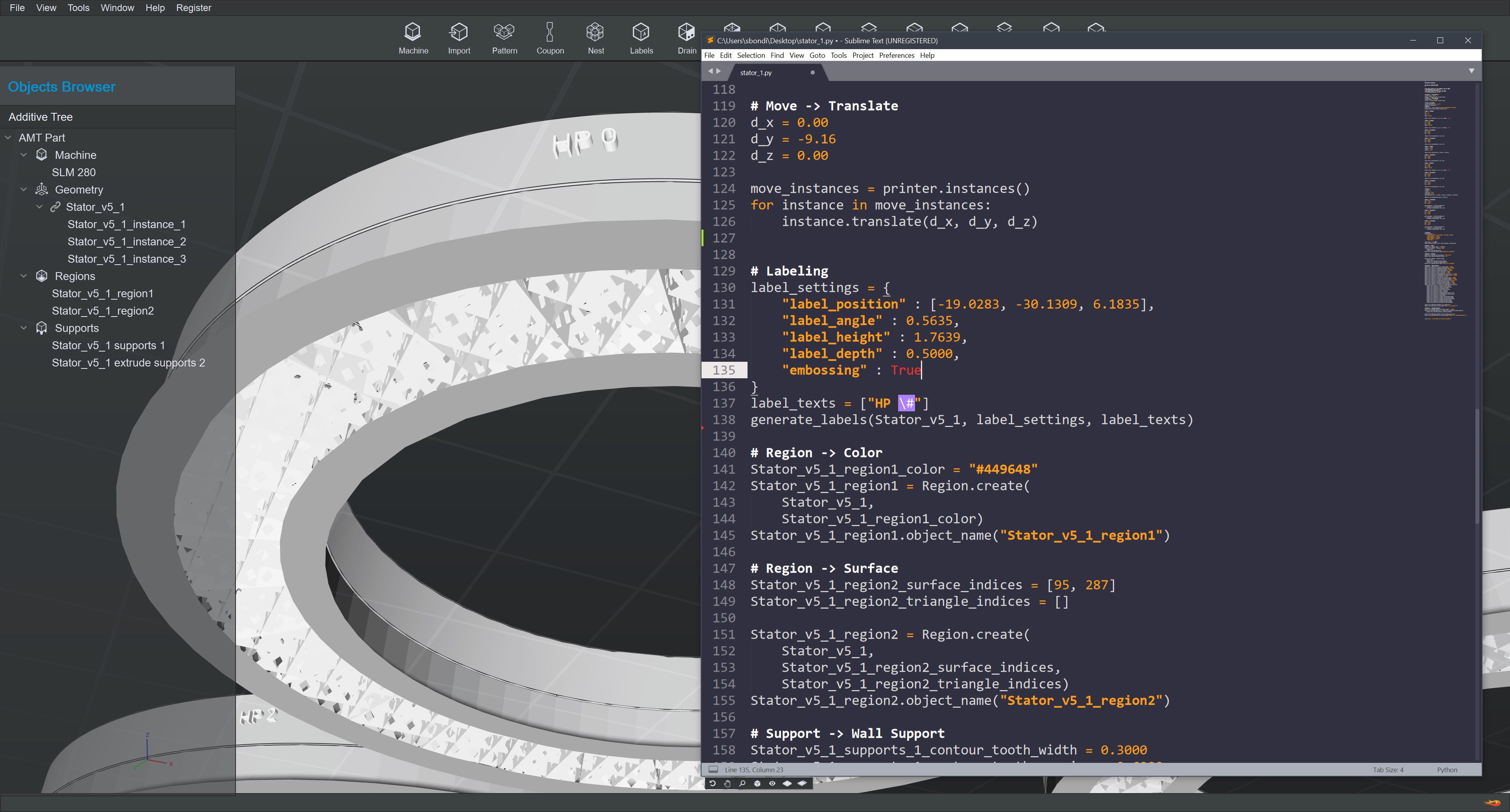
Pillar 1
Traceability
Just about every part put into production requires some form of serialization or part marking to reconstruct life cycle from provenance. AM and its ability to make every individual part unique holds immense power in bringing new levels of traceability to manufacturers. Imagine the reduction in liability exposure of an automaker, and their ability to save millions of dollars in recall costs, as they individually identify the single failed electrical connector and trace it back to a specific lot/batch rather than issuing blanket recalls.
Unfortunately, today’s legacy AM software offers only crude, manual methods (if any) for adding traceability.
Dyndrite provides:
- Labels, serializing, part marking, and even QR code application. Technicians no longer need to manually and tediously specify the contents and location of these types of tags. And that means they’re no longer compelled to skip this step all together because of the overwhelming workload.
- Manufacturing travelers. To understand and follow a part through the entire manufacturing process one needs Manufacturing Travelers, documents that provide a build pedigree. Today, most documents are manually created, on a build-by-build basis, instead of being auto generated. These documents tend to query and catalog similar information. For example, a user may automatically track the center of mass of each part in the coordinate system of the machine and tie it to a specific printhead or laser tool.
- Tracking outputs. Measuring outputs from the build, whether the key dimensions of a part or the physical properties of tensile specimens/powders, output tracking is not only crucial to understanding the characteristics of your parts, but helps maintain traceability for the purposes of repeatable quality. All of these measurements must also be tracked and recorded in a manufacturing process. For more insight into the build qualification and calibration process, visit our Process Qualification & Calibration page.
These three capabilities remove barriers and friction to traceability by automating once manual processes. To scale a production process to thousands, if not millions of parts, users cannot, for example, be expected to click and manually type numbers into a dialog box, or use a simple CSV. Serializing parts must be a fast, flexible, and automated process. It must be taken into consideration starting from the design and integrated with a database, be it a spreadsheet or full-blown MES or ERP solution.
- Available materials (new materials, multi-material)
- Printable parts (small features, thin walls etc.)
- Quality of parts (material homogeneity, surface profile)
- Whether or not the process requires aids such as supports
Pillar 2
Repeatable Quality
Manufacturers require processes that work job after job. Unfortunately, any AM technician today can attest to the variability of the process which makes repeatable quality extremely difficult or nearly impossible. The following are some examples of what technicians face:
- Each print/build setup process starts manually from square one. Technicians rarely reuse any prior work and must resolve the same issues over and over again. On top of this, each technician sets up build jobs differently and introduces variability into the manufacturing process.
- Parts must be oriented, nested, supported, and sliced in the same way every time. Due to the lack of reuse of prior work, subsequent builds also come with their own form of variability.
- Builds typically start with an STL input, a linear surface tessellation approximation of native CAD data. STLs are a fundamental flaw in the AM process. STL repair is so common that entire companies have grown up with this as their primary value proposition. While tolerable for prototyping, or one offs, the moment a manufacturer has to stop and fix something pathological, it's no longer a repeatable or automatable process. Additionally, manually selecting triangles to assign parameters, or supports not only wastes time, but makes things even less repeatable.
- AM machines, even those of the same model, operate slightly differently, almost like a fingerprint. Users need a way to address this variability, modifying toolpaths to make it possible to maintain consistent quality even between the same types of machines. A process can only begin to be considered a production process if you have about 5-10 machines in use and have six sigma compliance across those machines. If each of those 5-10 machines deliver a difference in part size, quality, and tolerance, then you end up with an extremely costly number of issues to solve.
Variable quality is a non-starter when considering production. Engineers and technicians need software tools that eliminate manual operations and file repair, address machine variability, while enabling automation through abstraction.
- Available materials (new materials, multi-material)
- Printable parts (small features, thin walls etc.)
- Quality of parts (material homogeneity, surface profile)
- Whether or not the process requires aids such as supports
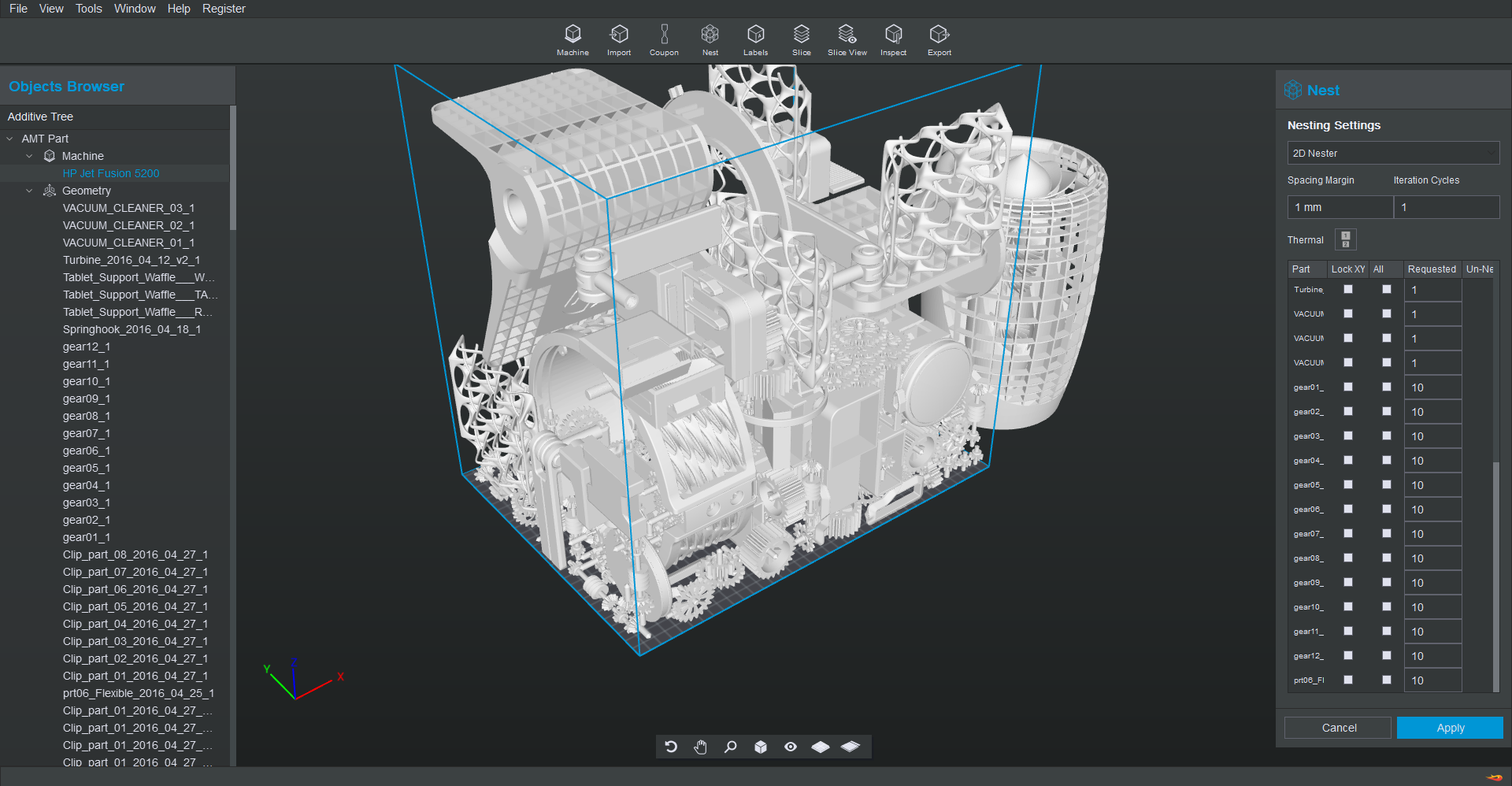