You have a clear vision of what to create with your metal 3D printer. You just need to control the laser.
As a materials or process engineer, you have clear goals: effective thermal management and precise control over laser properties and toolpath geometries. Dyndrite's tools empower you to combine mathematical, geometrical, and computational expertise with your knowledge of chemistry, physics, and mechanics. With Dyndrite LPBF Pro's part querying and toolpath control features, you can address the physical aspects of laser-based 3D printing, create innovative material parameter sets, and achieve what was once considered impossible.
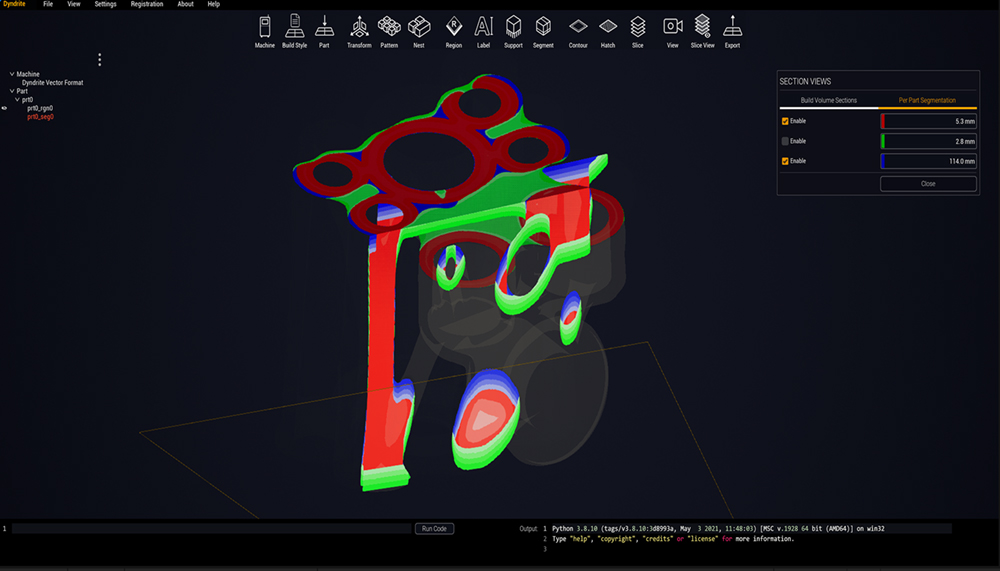
Use Dyndrite LPBF Pro to print with challenging materials such as GRCop-42.
Get the most flexible, controllable, and highest-performing toolpath generation tool available for maximizing the output of your industrial 3D metal printer. Your innovative parameter sets and strategies are your intellectual property.
Address manufacturing problems
- Limited selection of available materials
- Hard-to-print parts
- Inefficient or slow build rates
- Unacceptably poor part quality
Get greater design freedom
(without extensive DfAM)
- Complex geometries
- Intricate internal features
- Avoid part warping
Account for print features
- Extremely low print angles
- Horizontal inner diameter holes
- High aspect ratios
- Thin walls
- Fine surface finish
Improve 3D metal printer efficiency
- Increase build throughput rates
- Lase the core every th layer
- Design for multi-optic systems
- Use high layer-height strategies
Take more control of your AM jobs
Materials and Process Development for LPBF is designed to help you take more control of your AM jobs. If you’re eager to move your AM projects forward, apply to join the Early Adopter Program today.