SOFTWARE
Additive Hardware Has Exceeded Its Software
Additive manufacturing is on the precipice of becoming a widely adopted production process. Unfortunately, it suffers from an outdated software foundation.
For those creating the machines, tools, and factories of the future, the software foundations they’ve come to rely upon lack the power to crunch their data, the freedom to innovate in their own application space, and the control necessary to deliver their unique value propositions - without having to reveal their Intellectual Property (IP).
For the customer this has led to excruciatingly slow job processing times, overly complex non-integrated workflows, a lack of design-to-production automation tools, and costly OpEx.
The high barriers to software entry leave OEMs with few options: Those that can afford it build their own small/siloed software teams and proprietary applications. Those who cannot opt for sub-par software from vendors and are often unable to protect their IP.
For innovation in the space to thrive, we need fundamental change.
Watch the Video of SLM Solutions CEO
INTELLECTUAL PROPERTY
We Don't Want Your IP.
You Are the Best At Running Your Machine.
Licensing additive software for your machine shouldn’t mean that you have to reveal your unique intellectual property. A core tenet of Dyndrite is to help you protect your machine, metallurgy, materials, process, simulation and toolpath IP by delivering toolsets and APIs that allow you to keep your trade secrets, well... secret.
Learn About Dyndrite Solutions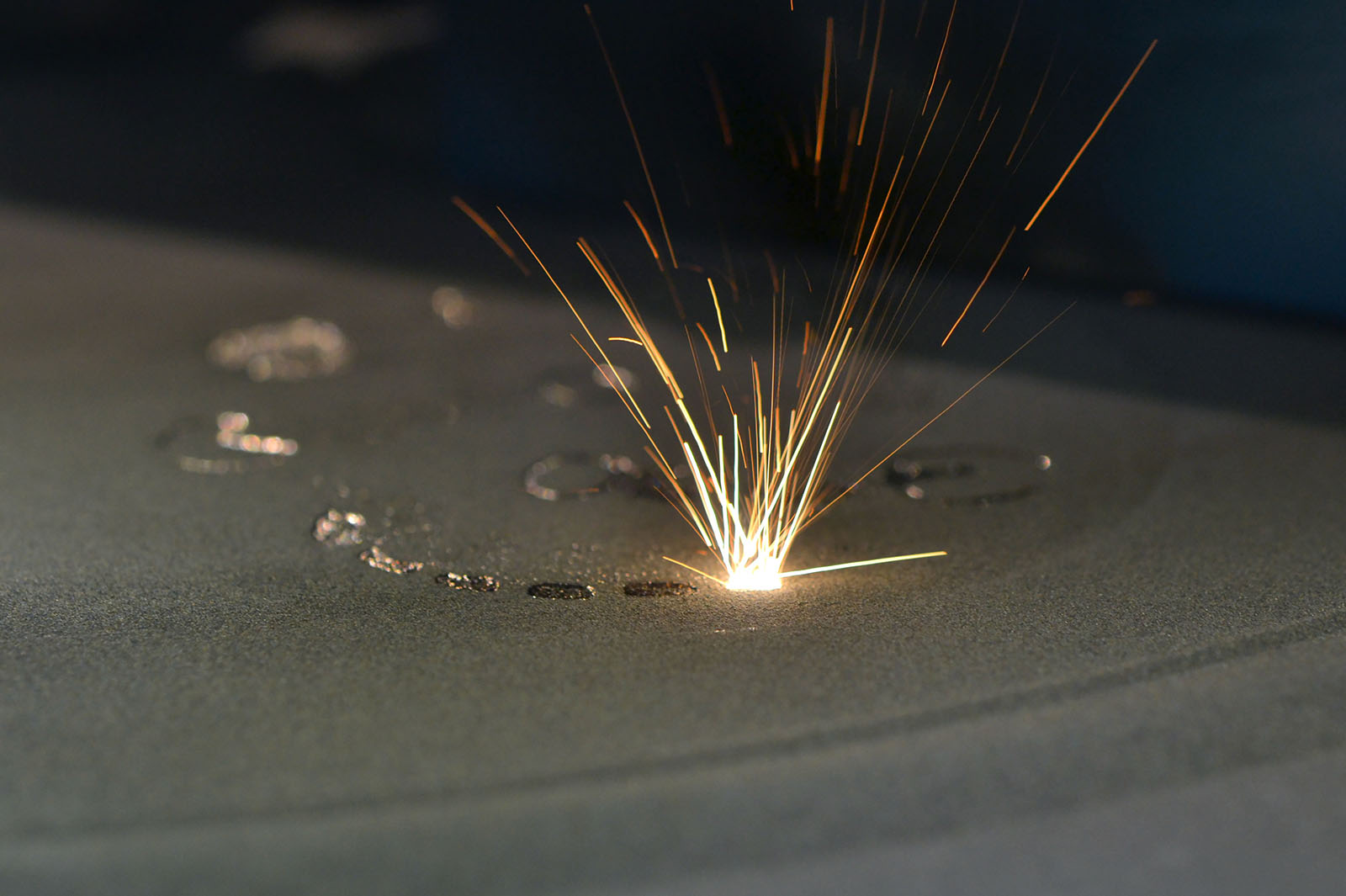
DATA
A Data Tsunami Is Coming. CAD Data is Preferred.
Build volumes, printer resolutions, and 3D part data size are all increasing at a cubic rate. Parts are getting more complex. Users are expecting per voxel controls, wanting finer features and more sophisticated toolpathing.
Like any other digital process, additive manufacturing excels when given more data. Unfortunately, today’s legacy software tools, workflows, and the formats they rely on were never designed to handle or process this type or amount of data. Some leading applications struggle to open, let alone process, today’s engineering design and manufacturing files.
For the digital manufacturing industry to advance, this has to change.
Learn About the Dyndrite EngineManufacturing Data File Sizes
COMPUTE
The Industry Is Ignoring Powerful Computing Resources Making Customers Waste Valuable Time & Money
Legacy software tools are letting powerful CPUS and GPUs sit with idle computing cycles. As users struggle to prepare and process files, it is not uncommon for a technician to wait hours, or even days for a file to prep - sometimes taking longer than it actually takes to print the file- this is unacceptable.
GPUs Are Powerful Computing Solutions. But They’re Primarily Used to Render Pretty Pictures
GPUs are a source of tremendous computing power that enable parallelized, scalable performance. Unfortunately, most CAD/CAM software only leverage the GPU to render photorealistic images, leaving most of the heavy geometry and file processing to the CPU, and not even in a multi-threaded manner.
Programming for the bare metal on CPUs, and GPUs is hard, and requires specially trained programmers, experience, and know-how. At Dyndrite we knew it was our goal to not only harness these computing resources, but to democratize access to this power.
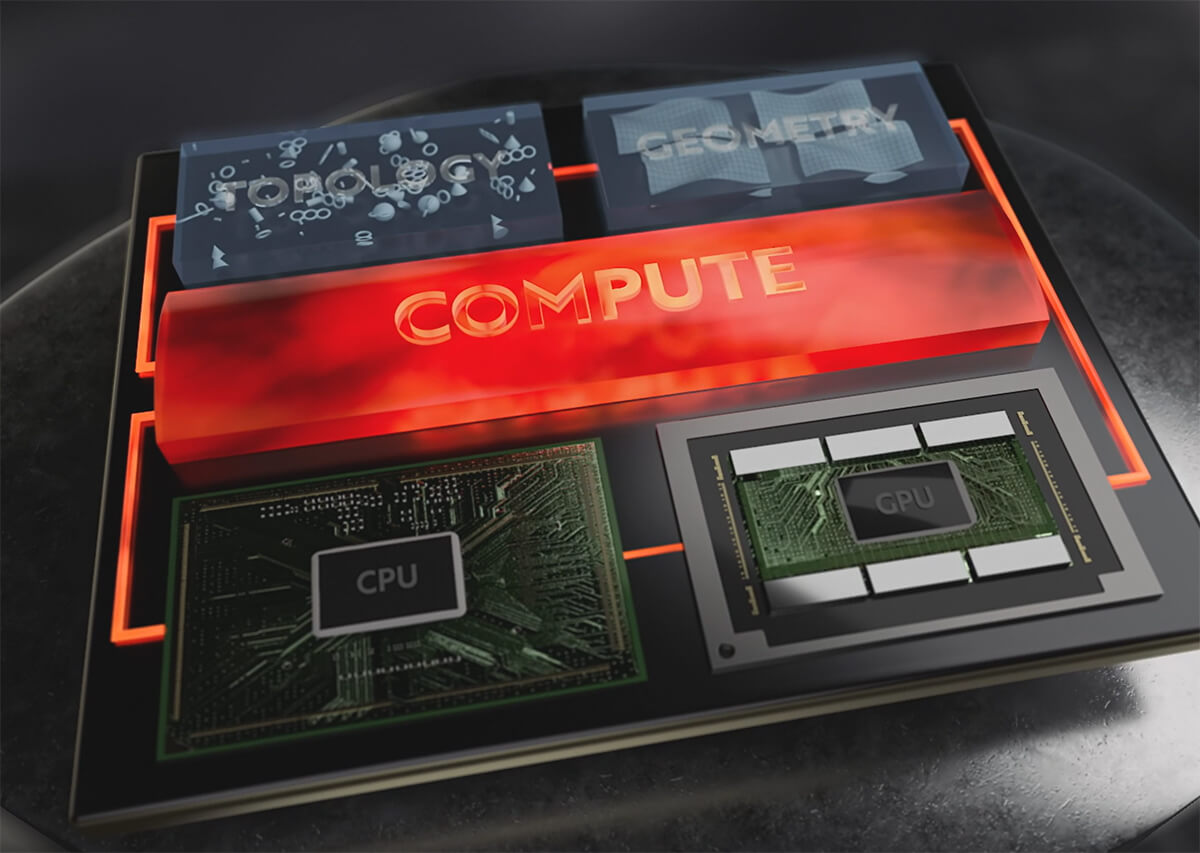
AUTOMATION
There’s a Complete Lack of Automation and Extendable Language for Communicating With Others
Automation is the next frontier for digital manufacturing. Yet, AM remains a mostly manual process. There exists few means and methods to automate end-to-end production processes and enable vendor-to-vendor communications.
Solving both these issues opens opportunity and enables collaborations that bring the collective strength of an industry to solving critical customer issues.
Communication starts with a common “lingua franca”. A language that enables anyone to participate and add value - without having to reveal their know-how or secret sauce. Through a pay-it-forward mechanism with Dyndrite, multiple and varied parts of the pipeline can be solved and plugged in to enable end-to-end automation.