The Next 30 Years of Additive Manufacturing Will Be Defined by Production
There are two pillars to manufacturing success: Repeatable Quality and Traceability. AM has struggled to scale to production-grade use cases due to a number of issues that don’t allow AM to comply with these two pillars.
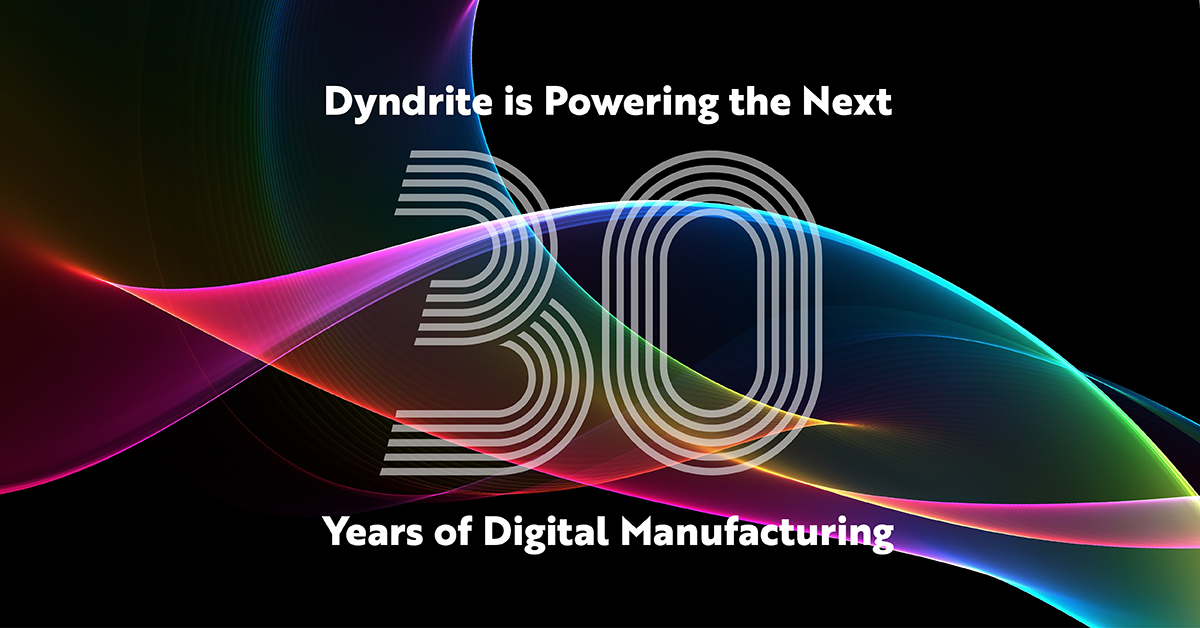
Part 1: Additive Manufacturing and the Two Pillars of All Production Processes
By Shawn Hopwood, Chief Marketing Officer, Dyndrite
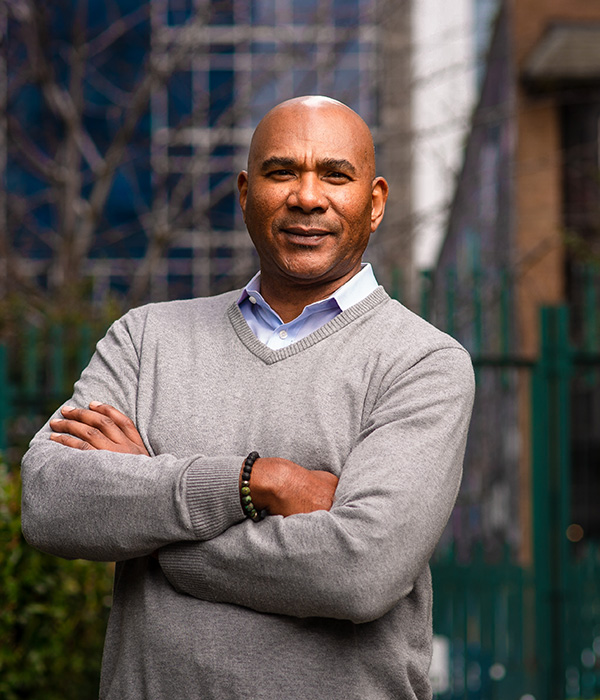
There are two pillars to manufacturing success: Repeatable Quality and Traceability. AM has struggled to scale to production-grade use cases due to a number of issues that don’t allow AM to comply with these two pillars.
3D printing first came to market more than 30 years ago. In that time we have seen incredible innovation in 3D printing processes, new materials, and applications for 3D printing. We moved from rapid prototyping to short-run production and are now driving towards sustained serial production. Manufacturers now talk less about “3D printing” and more about “additive manufacturing” as the dream of ”from art to part” becomes reality.
For hardware innovation, it has been a good 30 years. The same cannot be said of the software side. While engineers talk about digital transformation, digital twins, and digital threads revolutionizing manufacturing workflows, those who work directly with 3D printing know the path from art to physical part is a multi-step set of manual operations, with significant holes and process shortcomings. In fact, software is the reason that AM lacks two of the most important pillars of manufacturing, pillars that one might assume digital manufacturing would excel in, repeatable quality and traceability.
Pillar 1: Repeatable Quality.
Manufacturers require processes that can be relied upon to faithfully work time after time, job after job. Unfortunately, using legacy AM systems any technician can attest to the variability of the process which makes repeatable quality nearly impossible. The following are some examples of what technicians face:
- Each build setup process starts manually from square one. The technician is rarely able to reuse any prior work and must resolve the same issues over and over again. On top of this, each technician sets up build jobs differently, and introduces variability into the manufacturing process.
- Builds typically start with an STL input, a linear surface tessellation approximation of native CAD data. STLs are a fundamental flaw in the AM process that inherently prevent repeatable quality. One of their issues, file repair, is so common that entire companies have grown up with this as their primary value-proposition. While tolerable for prototyping, or one offs, the minute a manufacturer has to stop and fix something pathological, it's no longer a repeatable or automatable process. Manually selecting triangles to assign parameters, or supports not only wastes time, but makes things even less repeatable.
- AM machines, even those of the same model, operate slightly differently, almost like a fingerprint. Users need a way to address this variability, modifying toolpaths to make it possible to maintain consistent quality between machines or the same types of machines. Something can really only be considered a production process if you have about 5-10 machines used and have six sigma compliance across those machines. If each of those 5-10 machines deliver a difference in part size, quality and tolerance, then you end up with an almost exponential number of issues to solve.
Variable quality is a non-starter when considering production. Engineers and technicians need software tools that eliminate manual operations, file conversions, file repair and address machine variability while enabling automation through abstraction.
Dyndrite is developing software that specifically hits these three blockers to repeatable quality:
- Python enables you to codify manufacturing rules, codify best practices, make feature/part families, and most importantly is a way to guarantee repeatable quality in such a complex process.
- Why fix the STL, when you can import the native CAD directly. No need to bandaid a problem that shouldn’t exist in the first place.
- Users can use geometric queries instead of manual triangle selection to enable repeatability, and parametric abstraction.
- Software is needed to fully control toolpathing parameters to account for machine variability to improve part-build consistency and reduce variability.
Pillar 2: Traceability.
Another critical pillar of production is traceability. Just about every part put into production requires some form of serialization in order to reconstruct provenance. Here as well, AM and its ability to make every individual part unique holds immense promise in bringing new levels of traceability to manufacturers. Imagine an automaker being able to save billions of dollars in recall costs by being able to individually identify the single failed electrical connector batch over having to issue blanket recalls.
Unfortunately, today’s legacy systems provide crude, manual methods (if any) of adding any form of traceability.
- A key way to maintain traceability down to the part is the use of labels/serializing QR codes. The complete lack of labeling automation in the AM process means that technicians need to manually specify the contents of these types of tags, and their location on each part being manufactured.
- Manufacturing travelers are key ways to understand and follow a part through the entire manufacturing process. They provide a build pedigree, and are also manually created on a build-by-build basis. For example, users need to be able to track the center of mass of each part in the coordinate system of the machine.
- Measuring outputs from the build, whether measuring the key dimensions of a part, or the physical properties of tensile specimens/powders, is crucial for not only understanding the characteristics of your parts, but helps in maintaining traceability for the purposes of repeatable quality. All of these measurements must also be tracked and recorded in a manufacturing process.
All of the above three concepts are either blockers to traceability or add friction to making a process traceable because they are manual processes. In order to scale a production process to thousands if not millions of parts, users cannot, for example, be expected to click and manually type numbers into a dialog box. Serializing parts must be a fast, flexible and automated process. It needs to be taken into consideration starting from the design, and must be integrated with a database, be it a simple spreadsheet or full blown MES or ERP solution.
Dyndrite is committed to providing a new software foundation that fulfills the promise of AM in production. As we drive forward, we will be going deeper into these topics including interviews with key participants and partners in the industry. Stay tuned for Part 2.
Special Thanks:
Anthony Graves of HP Software for allowing us to pick his brain.
Philip DeSimone of Carbon for allowing us to steal some of his brilliant ideas.
Find out more on this topic by attending Dyndrite Developer Conference 2021, April 20-21 (virtual event)
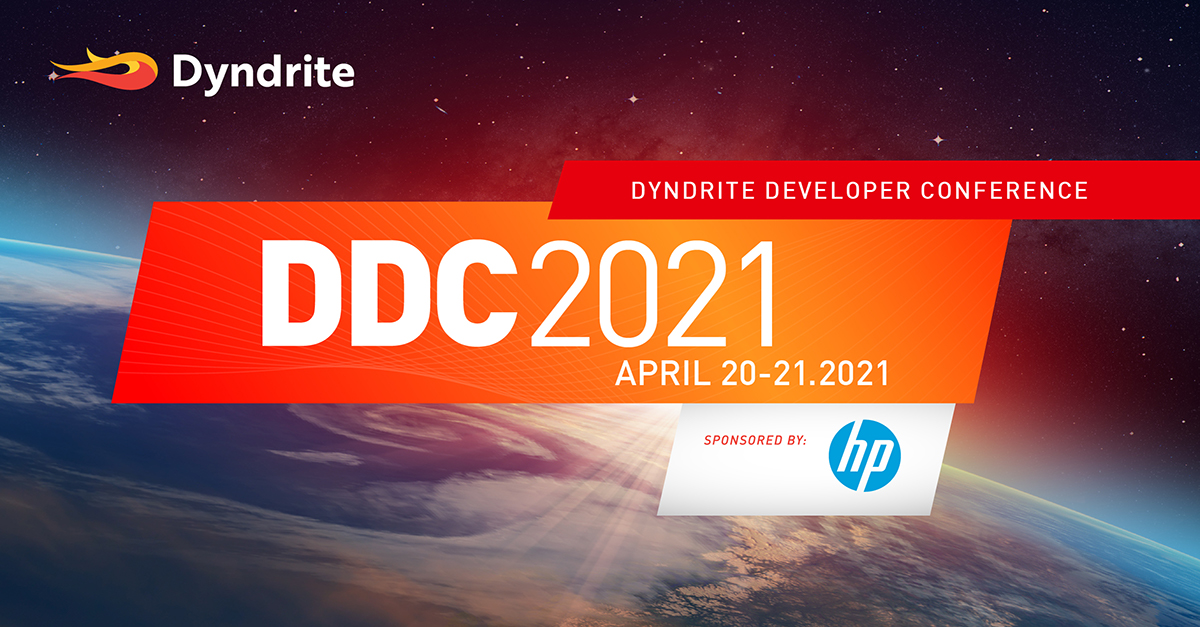