Is This a New Chapter for Additive Manufacturing?
On April 21-22, 2020, Dyndrite hosted the Dyndrite Developer Council 2020 online event. The lineup of speakers from Dyndrite Developer Council members spanned the additive and engineering software industries, including HP, NVIDIA, SLM, EOS, 3D Systems, Renishaw, Ansys and many more.
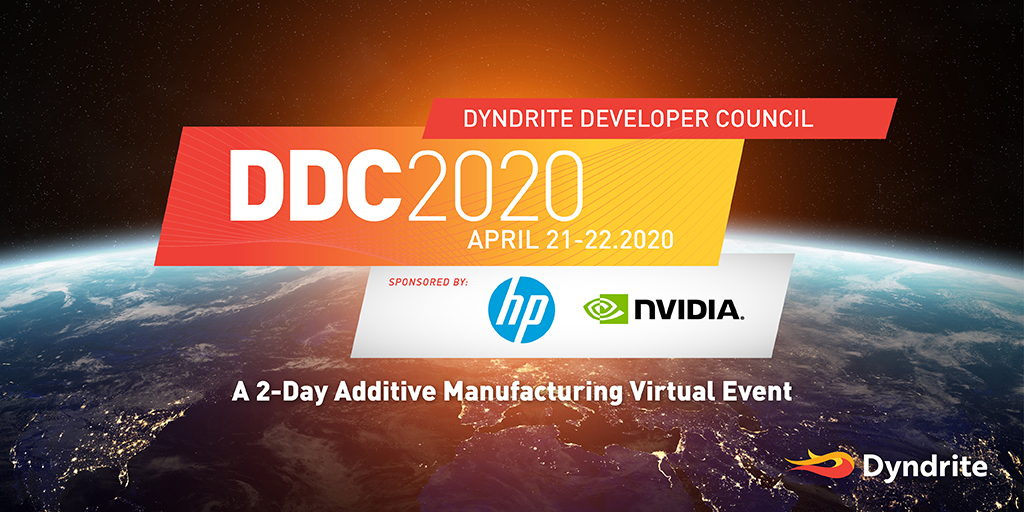
The event enabled industry leaders to present to attendees from companies such as Blue Origin, Collins Aerospace, BMW, Exxon Mobil, who exchanged views and discussed new opportunities the industry is facing.
The response by the additive industry to the need for PPE devices during the COVID-19 crisis was top of the list for several companies. While presenters talked about the work that had been done to achieve short-term fulfillment into the disrupted supply chain, there was more discussion about how this unusual event has reinforced the value of additive versus traditional manufacturing.
Ryan Palmer, SVP and Global Head of Software at HP, brought this up during his keynote session on the first day. He noted that pretty much all traditional manufacturing of parts uses “Processes optimized for steady state cost efficiency rather than agility” including that each production line was focused on specialization and was centralized rather than distributed production. However, additive showed it has the agility to respond quickly and in an unprecedented way, and fill a gap precisely when it was needed.
Palmer went on to show how the teams at HP managed to design, test and produce PPE equipment with hundreds of production parts being distributed within 7 days, an effort that could barely be matched by traditional production techniques. He described this as a “true watershed moment” for the industry.
“We have a unique, potentially a once-in-a-lifetime opportunity to change the trajectory and the impact this industry has on the world forever,” said Palmer. “When faced with global changes, agility and velocity are the absolute best capabilities you can have. COVID has given us a tremendous opportunity to identify key products that can be produced with a digital supply chain.”
During the final panel session hosted by ex-CEO of Autodesk, Carl Bass, senior leaders from SLM, HP, Exone, EOS, Renishaw, and Dyndrite were asked what they are doing differently as a result of the crisis and to discuss a longer term view of what the industry as a whole needs to do to leverage this moment.
Meddah Hadjar, CEO of SLM, led the responses by pointing out that to address the COVID-19 crisis the company began networking, making alliances with companies and institutions they had never collaborated with before, and through that were able to address the situation, share IP in some cases.
He continued: “When we talk about competitors we are really in the same technology field. We are looking at how do we push this technology beyond from what it is? How do we make it mainstream? And make it really the norm versus the exception.”
Does the Industry Need STL Anymore?
Another common theme was about the restrictions that the long-enduring mesh based formats like STL continue to impose on productivity, throughput and accuracy. Dyndrite CEO, Harshil Goel, during his keynote speech termed STL as being ‘pathological’ to fix, and that the format itself is preventing additive manufacturing from being a production-grade process. Indeed 67% of respondents polled during the event said they would like to move away from STL.
Len Wanger, CTO, Impossible Objects in his presentation called ‘Let’s Kill STL’ further emphasized that the STL file needs to go, and be replaced by direct CAD-to-Print technology. He listed out the common problems with STL which includes invalid files that need repair, very basic information without meta-data or GD&T, the ‘tesselation’ effects on computationally-accurate 3D data, lack of security, and just the overall bad user experience. Working with Dyndrite, Impossible Objects is developing secure chains of file custody from CAD through to print.
Data Explosion is a Barrier to Productivity
The STL is only one part of the issue related to exploding data sizes in additive manufacturing data. Additive manufacturing data problems was an underlying theme among a number of the talks given. Goel pointed out: “We are seeing 10GB CLI files and 4TB PNG folders that are not practical or smart. We need software or a system to on-the-fly expand this manufacturing data. In fact, we have run onto various printer manufacturing companies who would essentially have to spit out about 4 PB of data” if they were to reach their build volume and resolution requirements.
By eradicating STL, and by driving computing power closer to the edge, we will enable additive software to become production grade and resolve its data problem.
Another factor that is preventing the evolution of additive into production-grade levels is the lack of computing power available to handle the large processing tasks required in the industry. Mike Geyer, Industry Marketing Director at NVIDIA, feels that his company, in collaboration with Dyndrite, has the solution to the problem with the addition of GPU computing in the manufacturing industries.
While GPUs have a strong history in gaming devices and real-time rendering, NVIDIA and Dyndrite are bringing high performance GPU computing power directly to manufacturing, especially additive. According to Geyer, manufacturing as a whole is pretty stodgy, inefficient and many times very wasteful industry, and, according to him, “Only the most determined, the most innovative, the most flexible companies are going to be the ones that get ahead and use the current situation as a way to springboard into a new future.” Adding GPUs to that future is the way forward.
The Need for New Industry Standards
Goel also pointed out that new standards in the industry are a requirement to deliver automation and production in additive, which is Dyndrite’s mission:
“The whole idea here is can we create a unified standard to pull all these [Developer Council members] together so that the user has a better experience,” Goel stated.”The key to all of this is a), using Modern Compute and b), making sure that the industry is setting a standard. We can’t possibly have 30, 40 or 100 separate printer companies all with different competing standards.”
Martin Stueur, SVP of Software, EOS, agreed during the final executive-level panel hosted by Carl Bass, that the additive industry needs to work together to create standards, even while being competitive.
“There is this funny picture which is like a cartoon of 2 donkeys tied together with a rope and both are running to a haystack on the opposite sides instead of both donkeys going together to one haystack and eating it together and then going together to the other,” He comments. “And I think we, as an industry, should join in terms of what are the standards that we are adhering to in order to make this market faster and bigger for us.”
The Toolpathing Panel session, hosted by Steve Walton, Head of Product, Dyndrite, brought together technical experts from companies including Aurora Labs, Renishaw, Aconity3D, Impossible Objects, and N.E. Foundry Tech. The aim of this session was to set the groundwork for creating toolpathing standards for the industry and how to move towards that.
In a lively discussion the panelists generally agreed that standards in toolpathing are needed but there is a dilemma. How much should companies innovate versus standardize?
Kevin Brigden, additive manufacturing applications engineer at Renishaw, said “I think one of the biggest challenges this industry faces is the continuous pull in two directions, one to innovate and one to standardize. And one things for sure is that if every hardware vendor is going off and doing something quite different and innovating in different ways, there’s a real risk that everything could become so segmented that the industry as a whole can’t grow.”
A New Approach to Additive Software
EOS’ Rudiger Herfried, Product Line Manager - Data Preparation, announced during his session that EOS is delivering a new Open Software Architecture, which connects the EOSPRINT and EOSCONNECT software development toolkits with the Dyndrite kernel.
“Our goal is that the customers don’t use our user interfaces for our software. The goal should be for customers to use, for example, just the Dyndrite platform and everything else to control the machines is running underneath,” he said. “So the single user interface for the customer is the Dyndrite platform.”
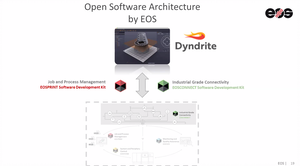
EOS presentation during DDC2020
Now is the Time for Innovation
As Todd Grimm pointed out in his keynote, innovations in additive are still underway despite concerns about the immediate economic future.
SLM Solutions' Sheldon Winthrop featured the company's latest quad-laser system during his vendor presentation, noting that each time the amount of lasers in a platform are doubled, the system can produce double the amount of components, at double the build rate, with a cost savings of 35-40%.
Plural also took the opportunity to announce its new Spectral 30 FDM printer during DDC2020. This innovative system delivers a four-nozzle system and integrated control unit that can print 4 different jobs at a time, using different materials. It also has integrated print servers, web cam monitoring and dryers for greater throughput of parts.
Rising Above the Status Quo
Turning finally to the keynote by industry consultant, Todd Grimm, he had an important and uplifting message. After the current crisis, he warns against going back to the status quo.
“I call this ‘Having your back against the Status Quo Wall,” says Grimm. “What this means is, using status quo situations as leverage so that you need to do things differently. Say your supply chain broke badly during this. If you go to status quo that supply chain problem will still exist.”
Are we at a New Chapter for additive? We believe so and the presentations and panels at the Dyndrite Developer Council 2020 seem to agree.
There is all this and many more session recordings of Dyndrite Developer Council 2020 can all be viewed here. As you can see, there’s a lot to hear and learn!
Find out more on this topic by attending Dyndrite Developer Conference 2021, April 20-21 (virtual event)
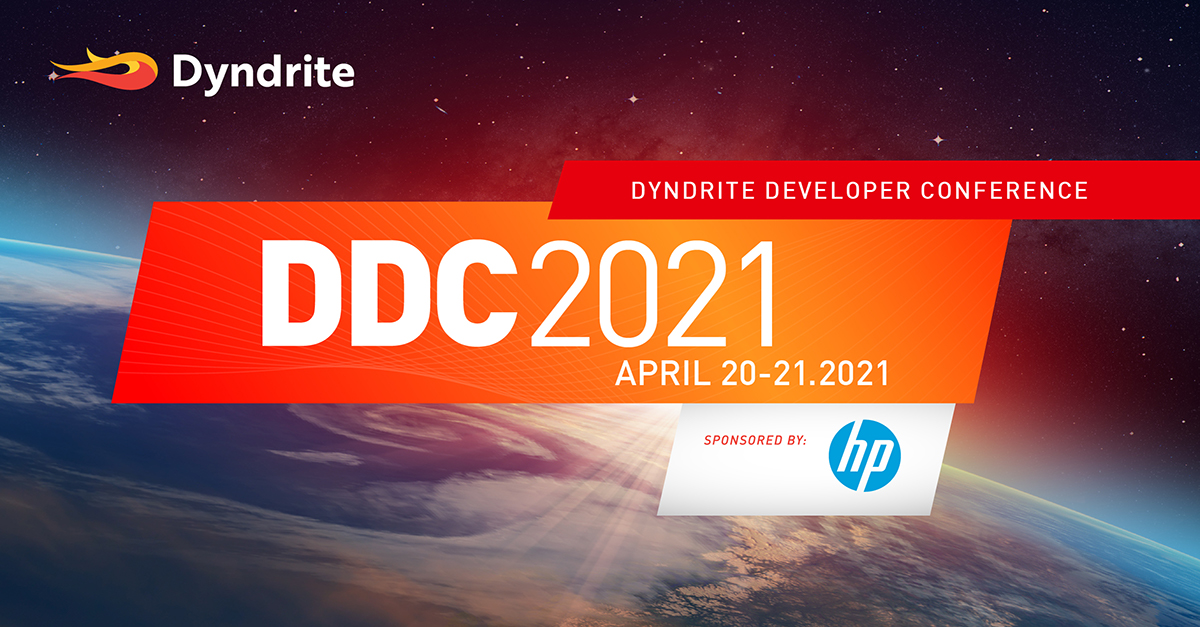